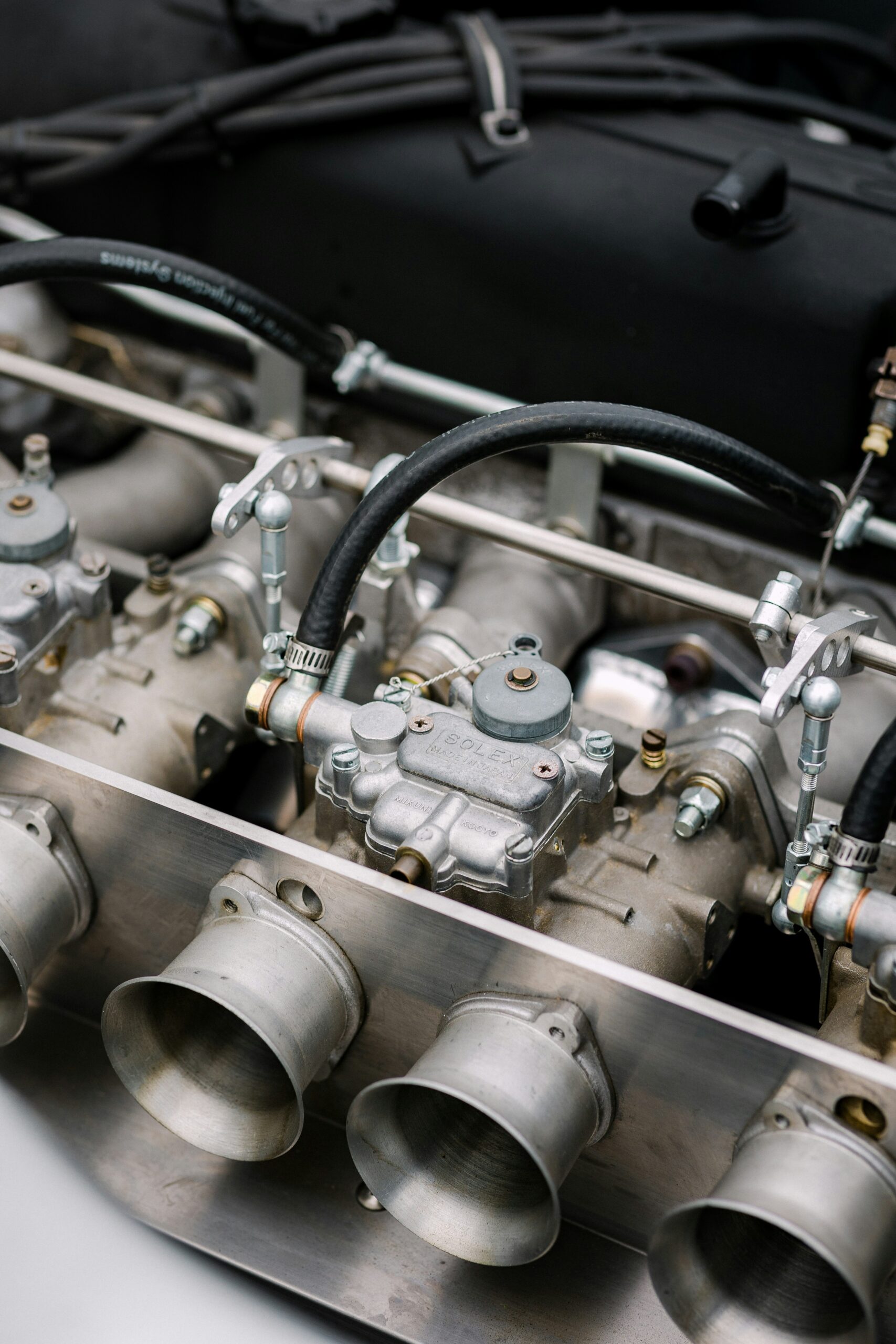
As the world increasingly turns to alternative fuels in response to growing environmental concerns, traditional engine designs must adapt to accommodate these new energy sources. Alternative fuels like biofuels, natural gas, hydrogen, and electricity are gaining popularity due to the global push for sustainability and reducing carbon emissions. The widespread adoption of these fuels presents unique challenges for the internal combustion engine (ICE), which has long relied on gasoline and diesel. Adapting traditional engine designs for alternative fuels is crucial for a smooth transition to greener energy solutions. Manufacturers are making significant strides to ensure engines run efficiently on these new fuels.
The Importance of Adaptation in Engine Design
Adapting traditional engine designs for alternative fuels is critical for meeting environmental regulations and improving fuel efficiency and performance. Engine manufacturers design traditional engines, specifically those for gasoline and diesel, to run on specific fuel types. They optimize internal components—such as the combustion chamber, fuel injectors, and exhaust systems—for conventional fuels. When shifting to alternative fuels, these components must undergo modification or replacement to ensure optimal performance, fuel efficiency, and minimal emissions.
The primary challenge in adapting engine designs lies in the differing properties of alternative fuels compared to conventional gasoline and diesel. For example, biofuels and ethanol have different chemical compositions and combustion characteristics, which can affect the engine’s combustion process. In contrast, hydrogen and natural gas require different pressure and storage systems due to their gaseous nature. Furthermore, the transition to electricity necessitates shifting to electric motors, which have entirely different mechanical and electrical systems than traditional engines. Thus, adapting engines for alternative fuels requires a comprehensive understanding of the fuel properties and an engineering approach that ensures compatibility without sacrificing performance.
Modifications for Biofuels and Ethanol Blends
One of the most common alternative fuels used in transportation today is biofuel, particularly ethanol blends like E85, which contain 85% ethanol and 15% gasoline. Ethanol is a renewable fuel derived from plant materials, making it a popular choice for reducing reliance on fossil fuels. However, adapting traditional gasoline engines to run on ethanol blends requires specific modifications to engine components.
Biofuels have a higher ethanol content than traditional gasoline, which means they have a lower energy density. Ethanol can impact fuel efficiency, as vehicles may require more fuel to achieve the same range as gasoline-powered ones. To compensate, engine manufacturers often modify fuel injectors to deliver more fuel, improving performance with ethanol’s lower energy content. Additionally, manufacturers change the fuel system to ensure the engine can handle ethanol’s more corrosive properties than gasoline. Since ethanol can degrade certain materials, such as rubber seals and gaskets, they often use more durable materials to prevent damage to engine components.
Another essential modification is adjusting the engine’s compression ratio. Ethanol has a higher octane rating than gasoline, which means it can withstand higher compression ratios before igniting. By increasing the compression ratio, engineers can enhance the engine’s efficiency and performance when running on ethanol. These adaptations allow traditional gasoline engines to run efficiently on ethanol blends, but they still require ongoing research to optimize the process and ensure long-term durability.
Adapting Engines for Compressed Natural Gas (CNG)
Compressed natural gas (CNG) is another alternative fuel that has gained traction due to its lower emissions and relatively low cost. CNG primarily contains methane, which is stored in high-pressure tanks. Many consider it a cleaner fuel than gasoline and diesel, as it emits fewer pollutants like nitrogen oxides and particulate matter. However, using CNG in traditional engine designs requires significant modifications.
One of the primary changes involves the fuel storage system. CNG is stored in cylinders under high pressure, often at 3,000 to 3,600 psi. Since traditional gasoline engines cannot accommodate this high-pressure fuel, manufacturers must modify the fuel tank and pressure regulators. The engine also requires changes to the fuel injectors and the intake system to accommodate the different combustion properties of methane. Methane has a higher ignition temperature than gasoline, requiring more precise control over the ignition timing to ensure optimal combustion.
In addition to modifying the fuel system, engineers must adjust the engine’s exhaust system for CNG’s cleaner emissions. CNG-powered vehicles produce lower levels of carbon dioxide, carbon monoxide, and particulate matter than gasoline engines, simplifying the exhaust system. Traditional components like catalytic converters may sometimes be smaller or less complex due to CNG’s cleaner emissions.
Transitioning to Hydrogen-Powered Engines
Hydrogen is one of the most promising alternative fuels for reducing carbon emissions, particularly in heavy-duty transportation. Hydrogen fuel cells produce electricity through a chemical reaction between hydrogen and oxygen, emitting only water vapor as a byproduct. Transitioning to hydrogen-powered engines presents unique challenges because hydrogen, being a gas, requires storage and transportation at high pressures.
Hydrogen-powered engines require significant modifications to traditional engine designs, primarily to accommodate the storage and fuel delivery systems. Unlike gasoline, hydrogen is stored in high-pressure tanks at pressures up to 700 bar (around 10,000 psi). Manufacturers must make these tanks from lightweight, durable materials to withstand high pressures and prevent leaks. The hydrogen fuel system must also have pressure regulators, valves, and pumps to control hydrogen flow into the engine.
In some cases, manufacturers use hydrogen in internal combustion engines (ICEs) as a direct replacement for gasoline or diesel, instead of integrating hydrogen fuel cells into electric vehicles (EVs).. These hydrogen-powered ICEs require adjustments to the ignition system, as hydrogen has a higher combustion temperature and a faster burn rate than gasoline. Engineers must carefully control the fuel-air mixture and ignition timing to ensure smooth operation and avoid engine knocking.
The Future of Engine Adaptations for Alternative Fuels
The transition to alternative fuels is ongoing and will shape engine designs in the coming years. As demand for cleaner energy grows, manufacturers will innovate to adapt traditional engines for new fuels like biofuels, CNG, hydrogen, and electricity. These adaptations are key to reducing carbon emissions, improving fuel efficiency, and helping the transportation industry meet sustainability goals.
In the future, we can expect advanced technologies, like hybrid systems that combine alternative fuels with traditional engines. These systems will allow vehicles to switch between fuels based on availability and efficiency. This will optimize performance and reduce environmental impact. As research progresses, engine designs will evolve, making the transition to cleaner fuels more efficient, affordable, and practical for various applications.
Adapting traditional engine designs for alternative fuels is essential for transitioning to a more sustainable transportation system. While challenges remain, the continued development and implementation of new technologies will allow for smoother integration of alternative fuels like biofuels, CNG, and hydrogen into existing engine designs. As manufacturers refine these adaptations, the transportation industry will be better equipped to meet environmental targets and pave the way for a greener future.